To design a monocoque chassis that improves the overall dynamic performance of the car it is important to understand what parameters that affect the performance. Key load cases that the chassis will experience will be determined and studied to understand how they impact chassis performance. A CAD-model will also be created to simulate the most important load cases and to gain knowledge about analysis of composite materials. Carbon fiber offers a lightweight construction and weight is an important parameter for electric vehicles. The main deformation modes and loads are longitudinal torsion, local bending around mounting points, and vertical bending. The project considers the design of elements of an isotropic material monocoque that has satisfactory torsional, hardpoint, and vertical bending stiffness. The isotropic analysis will used to gain insight and acquire knowledge about the behavior of shells and monocoque structures when subjected to a vehicle's applied loads. The isotropic modeling is then will used to set initial design targets for a full anisotropic composite analysis.
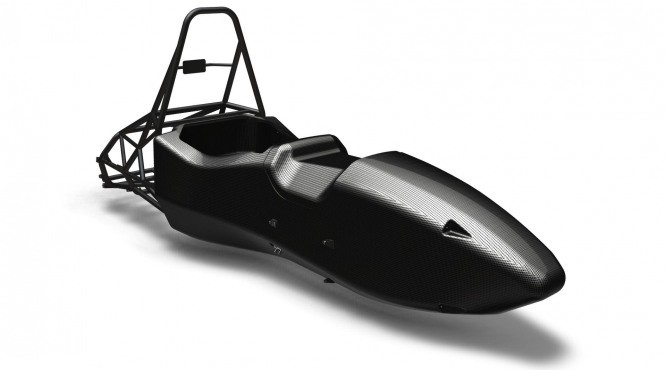
About Project Supervisors
Murat BÜYÜK, PhD